Perforación con martillo superior
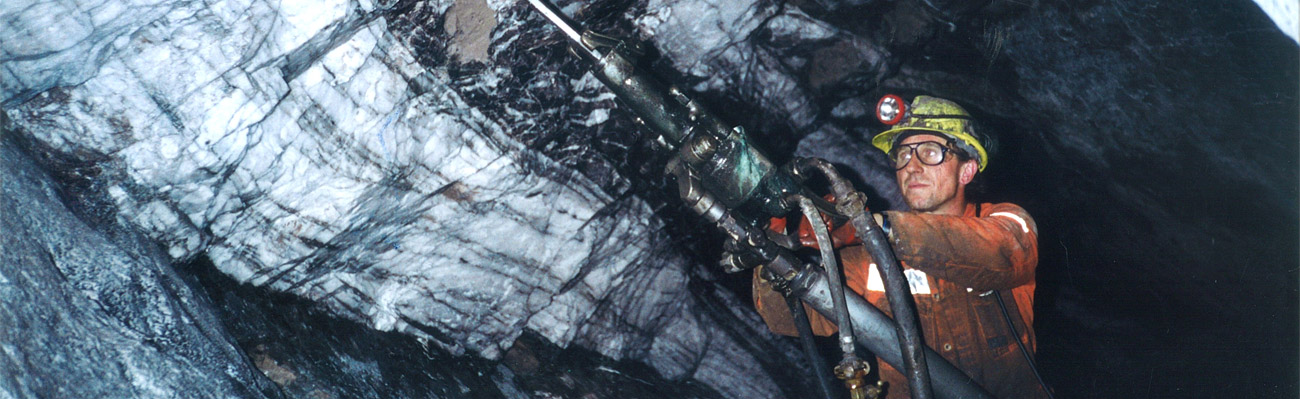
La disponibilidad, la variedad de diseños de brocas y el bajo costo operativo hacen que la perforación con martillo en cabeza sea un método ventajoso en muchas industrias diferentes, pero su aplicación generalizada inevitablemente conlleva una gama igualmente amplia de demandas y desafíos.
Versátil y flexible, la perforación con martillo en cabeza es utilizada por diversas industrias en todo el mundo. Podría decirse que la mayor ventaja de la perforación con martillo en cabeza es el tamaño, la disponibilidad y el bajo costo de las plataformas de perforación.
Las plataformas se pueden llevar a lugares de trabajo desafiantes, los contratistas de perforación generalmente tienen máquinas disponibles con poca antelación y tienden a ser más baratas que las plataformas de perforación DTH o rotativas.
En lo que respecta a los consumibles de perforación, la sarta de perforación con martillo en cabeza también es rentable, rápida de instalar y, gracias a la amplia gama de diseños de brocas disponibles, las brocas para martillo en cabeza siempre se pueden optimizar para las condiciones del terreno.
Sin embargo, las ventajas y posibilidades de la perforación con martillo en cabeza no significan sólo una amplia gama de posibles aplicaciones, sino también una gama igualmente amplia de clientes y demandas. Una mayor automatización, una mayor durabilidad de las brocas y una mayor eficiencia se encuentran entre los requisitos que deben cumplir los desarrolladores.
Ideal para minería y operaciones subterráneas.
Ideales para perforar pozos estrechos y cortos (de hasta 1 pulgada de ancho y hasta 40 m de largo) en roca dura, los taladros de martillo en cabeza se utilizan principalmente en minería, construcción y extracción de material rocoso.
La perforación con martillo superior debe ser la opción predeterminada para todos los orificios con un ancho de entre 1-1/2 y 4 pulgadas y una profundidad de hasta aproximadamente 30 m. Las condiciones del terreno no influyen tanto en la elección de la metodología de perforación, pero obviamente tienen un gran impacto en la selección de la herramienta. Una excepción a esto son las aplicaciones especializadas como la perforación de túneles, donde las condiciones débiles del terreno significan que es necesaria la perforación, lo que a su vez requiere automáticamente la metodología del martillo en cabeza.
Específicamente, el método del martillo superior es ampliamente preferido y utilizado en operaciones mineras subterráneas debido a la posibilidad de usar agua para eliminar los recortes. A diferencia de otras tecnologías, que funcionan con aire, esta mejora el entorno de trabajo subterráneo al minimizar el impacto del polvo de perforación en el aire.
Además de esto, la perforación con martillo en cabeza permite realizar una mayor cantidad de orificios más pequeños, lo que permite una voladura más precisa y controlada, algo que suele ser muy crítico en operaciones subterráneas.
Por último, la perforación con martillo en cabeza también es necesaria para las operaciones de empernado para asegurar túneles y, aunque las máquinas perforadoras utilizadas para el empernado y la perforación de producción pueden ser ligeramente diferentes, comparten la misma metodología de perforación y requieren las mismas habilidades de los operadores.
Los desafíos y limitaciones del método del martillo en cabeza
Si bien es ventajoso en muchas situaciones, el método del martillo superior también tiene sus limitaciones e inconvenientes. Uno de los mayores desafíos es el hecho de que a medida que la sarta de perforación pierde energía de percusión hacia la broca, las varillas más largas provocarán una mayor pérdida de energía y una menor eficiencia. La velocidad disminuirá hacia el final de los pozos más largos y, en algún momento, la perforación en el fondo del pozo (DTH) será completamente más ventajosa; los tamaños de pozos más grandes y/o los pozos más profundos significan que al menos se debe considerar la perforación DTH. incluyendo la posibilidad de agregar otro tipo de equipo de perforación a la operación.
Además, las repetidas ondas de choque del martillo hidráulico en los acoplamientos y las varillas de las sartas de perforación con perforador superior crean un desgaste continuo en los componentes, lo que significa que los taladros de martillo en cabeza generalmente requieren más consumibles a largo plazo. Esto también se aplica a las brocas que, en el caso de las brocas tradicionales, pueden necesitar ser cambiadas o afiladas varias veces durante una sesión de trabajo. El requisito de reemplazos o mantenimiento operados manualmente, a su vez, va en contra de una de las demandas más fuertes dentro de la industria, especialmente en la perforación subterránea, a saber, la demanda de una mayor automatización.
Además de esto, la perforación con martillo en cabeza permite realizar una mayor cantidad de orificios más pequeños, lo que permite una voladura más precisa y controlada, algo que suele ser muy crítico en operaciones subterráneas.
Por último, la perforación con martillo en cabeza también es necesaria para las operaciones de empernado para asegurar túneles y, aunque las máquinas perforadoras utilizadas para el empernado y la perforación de producción pueden ser ligeramente diferentes, comparten la misma metodología de perforación y requieren las mismas habilidades de los operadores.
Nuevas soluciones y viejas habilidades
Una de las peticiones más frecuentes de los operadores de perforadoras es la de contar con máquinas perforadoras automatizadas y controladas a distancia, capaces de perforar una sesión de trabajo completa antes de ser retiradas para la operación de voladura. Pero aunque en teoría los sistemas de control podrían permitir esto, se necesitan nuevas soluciones para que los consumibles lo permitan en la práctica.
Los taladros de percusión en cabeza flexibles y rápidos de configurar son ideales para perforaciones estrechas y cortas en roca dura.
"Las brocas de perforación tradicionales no pueden durar lo suficiente, pero Robit desarrolló brocas especiales con carburos recubiertos de diamante que pueden funcionar de la manera deseada. Eso significa que una broca puede perforar normalmente entre 3.000 y 3.300 pies (900 - 1.000 m). , y podrá mantener bien el rendimiento de perforación hasta el final de su vida útil sin necesidad de afilarlo", afirma Vuojolainen. "Si bien el coste unitario de la broca de diamante es claramente superior al de una broca TH habitual, ofrece una rentabilidad total por metro extremadamente buena".
Junto con las mejoras generales en la durabilidad de los consumibles de perforación, el deseo siempre predominante de los operadores de mejorar la eficiencia y el consiguiente aumento continuo de la potencia de perforación también están creando nuevas demandas para la sarta de perforación, especialmente las roscas. Como respuesta, el mercado está viendo nuevos diseños de roscas, como por ejemplo roscas macho/hembra con soporte de hombro, que muchos operadores han encontrado como una mejora con respecto a los diseños de roscas tradicionales.
Sin embargo, no es una innovación o aplicación específica la que decidirá la eficiencia y rentabilidad de la perforación con martillo en cabeza en un proyecto específico. Más bien, subraya Vuojolainen, se trata de la vieja habilidad de sumar todos los factores que determinan los costes y determinar el coste total de perforación (TDC). "El TDC es la suma del coste de productividad de la perforación en términos de tiempo y coste por metro (resistencia de la sarta de perforación)", explica.
El ahorro de energía es otro factor clave, ya que a veces la perforación se configura para perforar con presiones más altas, aunque no necesariamente sea necesario. En resumen, concluye Vuojolainen, en lo que hay que centrarse es en qué se puede hacer para aumentar la productividad aumentando la velocidad de perforación, evitando el tiempo de inactividad y gestionando la vida útil de los productos de desgaste.
Método de perforación con martillo superior
Una de las peticiones más frecuentes de los operadores de perforadoras es la de contar con máquinas perforadoras automatizadas y controladas a distancia, capaces de perforar una sesión de trabajo completa antes de ser retiradas para la operación de voladura. Pero aunque en teoría los sistemas de control podrían permitir esto, se necesitan nuevas soluciones para que los consumibles lo permitan en la práctica.
Los taladros de percusión en cabeza flexibles y rápidos de configurar son ideales para perforaciones estrechas y cortas en roca dura.
"Las brocas de perforación tradicionales no pueden durar lo suficiente, pero Robit desarrolló brocas especiales con carburos recubiertos de diamante que pueden funcionar de la manera deseada. Eso significa que una broca puede perforar normalmente entre 3.000 y 3.300 pies (900 - 1.000 m). , y podrá mantener bien el rendimiento de perforación hasta el final de su vida útil sin necesidad de afilarlo", afirma Vuojolainen. "Si bien el coste unitario de la broca de diamante es claramente superior al de una broca TH habitual, ofrece una rentabilidad total por metro extremadamente buena".
Junto con las mejoras generales en la durabilidad de los consumibles de perforación, el deseo siempre predominante de los operadores de mejorar la eficiencia y el consiguiente aumento continuo de la potencia de perforación también están creando nuevas demandas para la sarta de perforación, especialmente las roscas. Como respuesta, el mercado está viendo nuevos diseños de roscas, como por ejemplo roscas macho/hembra con soporte de hombro, que muchos operadores han encontrado como una mejora con respecto a los diseños de roscas tradicionales.
Sin embargo, no es una innovación o aplicación específica la que decidirá la eficiencia y rentabilidad de la perforación con martillo en cabeza en un proyecto específico. Más bien, subraya Vuojolainen, se trata de la vieja habilidad de sumar todos los factores que determinan los costes y determinar el coste total de perforación (TDC). "El TDC es la suma del coste de productividad de la perforación en términos de tiempo y coste por metro (resistencia de la sarta de perforación)", explica.
El ahorro de energía es otro factor clave, ya que a veces la perforación se configura para perforar con presiones más altas, aunque no necesariamente sea necesario. En resumen, concluye Vuojolainen, en lo que hay que centrarse es en qué se puede hacer para aumentar la productividad aumentando la velocidad de perforación, evitando el tiempo de inactividad y gestionando la vida útil de los productos de desgaste.
La principal distinción entre el método del martillo en cabeza y el método de fondo del pozo (DTH) es la ubicación de la fuerza de percusión dentro del aparato. En la perforación con martillo en cabeza, la actividad se concentra en la parte superior de la sarta de perforación, encima del pozo, mientras un martillo transmite ondas de choque cíclicas a la broca aplicando una fuerza de percusión sobre las barras o tubos de perforación (con las perforadoras DTH, el martillo se coloca en el fondo del pozo en la broca). El sistema de percusión golpea la barra de perforación con 2000 - 5000 golpes por minuto y la velocidad de rotación puede ser de 60 - 200 disparos por minuto. Los recortes se lavan desde el fondo del hoyo con aire o agua a presión.